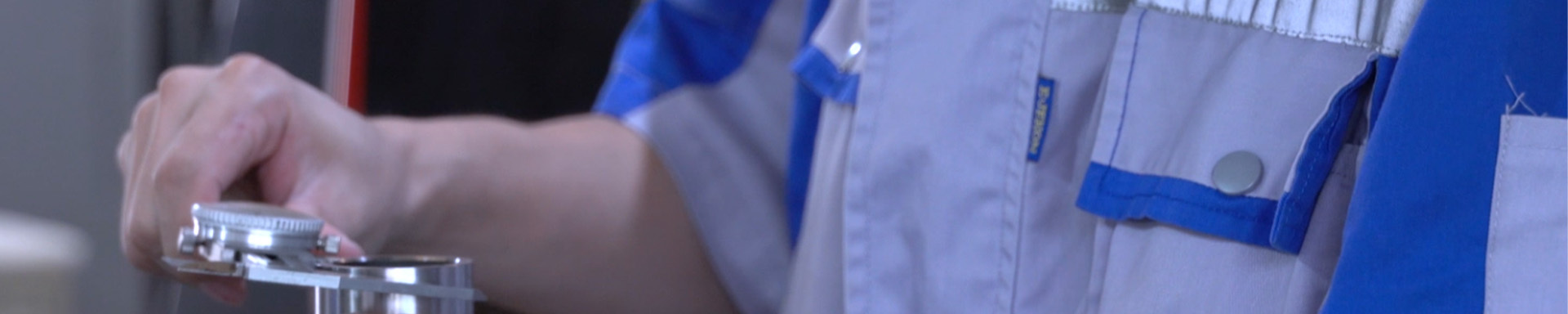
- Home
- >
- News
- >
- Industry News
- >
News
Steam turbine blades operate in extreme environments with high temperatures, corrosive media, and mechanical stresses. Over time, corrosion and wear degrade blade performance, leading to efficiency losses and costly maintenance. To address these challenges, Alloy 6B/UNS R30016 is a superior material for wear strips and protective overlays on steam turbine blades. This cobalt-chromium-tungsten alloy complies with AMS 5894, combining unmatched corrosion resistance, high-temperature stability, and mechanical durability. This article explores the root causes of turbine blade corrosion and the criteria for material selection.
2025/2/19, a Turkish customer sent an email, hoping that we could introduce the difference between our material and tungsten carbide. He said: "we use them in milk homogenization. original from german as tungstean carbide. can you recomend us your products much better tan tc mtrl?"
Under complex working conditions of high temperature, strong corrosion, and high wear, material selection directly determines the life and reliability of the equipment. Due to their comprehensive performance, cobalt-based high-temperature alloys have become "key materials" in the aerospace, energy, and chemical industries. This article analyzes cobalt-based alloys' applicable scenarios and alternatives based on industry technology trends and provides material selection references for industrial users.
When it comes to industrial machinery and applications, choosing the right bearing bush is crucial for ensuring longevity and performance. Bearing bushes are integral components that reduce friction between moving parts, providing smoother operation and reducing wear. As a leading bearing bush manufacturer, SYTOP is proud to offer a wide range of high-quality, wear-resistant bearing bushes designed to meet the demanding conditions of various industries.
Cobalt 12# Alloy is a cobalt-based alloy known for its outstanding wear, heat, and corrosion resistance. Ideal for industries requiring high durability, it excels in extreme environments.
In this article, we will explore what friction stir welding is, how it works, and the choice of tool material.
Cobalt Alloy 25, known as Haynes 25, Alloy L605, and UNS R30605, is a high-performance alloy designed for extreme environments. This alloy is widely used in the aerospace and industrial sectors.
On November 22, 2024, SYTOP finished a new batch of transition pieces seals designed for GE turbines. These high-performance seals, made from cobalt-based alloys, provide reliable, long-lasting protection against leaks in critical turbine systems. The new seals are engineered to withstand high pressures and temperatures, ensuring GE turbines' optimal performance and longevity.