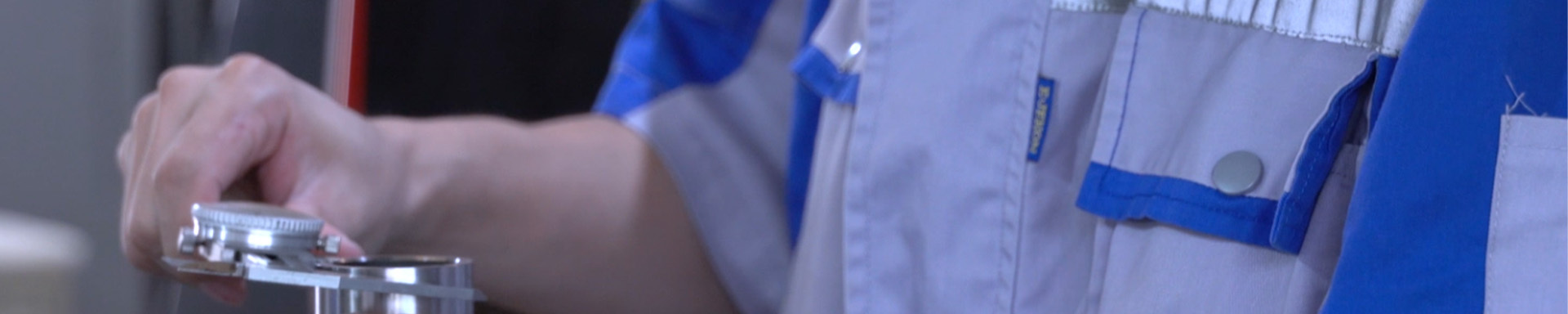
Why Choose Alloy 6B as the Material for Steam Turbine Blades?
2025-02-25 09:00Steam turbine blades operate in extreme environments with high temperatures, corrosive media, and mechanical stresses. Over time, corrosion and wear degrade blade performance, leading to efficiency losses and costly maintenance. To address these challenges, Alloy 6B/UNS R30016 is a superior material for wear strips and protective overlays on steam turbine blades. This cobalt-chromium-tungsten alloy complies with AMS 5894, combining unmatched corrosion resistance, high-temperature stability, and mechanical durability. This article explores the root causes of turbine blade corrosion and the criteria for material selection.
Causes of Steam Turbine Blade Corrosion
Stress Corrosion Cracking (SCC)
Prolonged exposure to high-temperature steam and cyclic stresses induces micro-cracks, accelerating material failure. SCC is particularly prevalent in blades subjected to wet steam with dissolved oxygen and chlorides.
Abrasive and Erosive Wear
Wet steam carries micro-droplets and particulates that erode blade surfaces, especially in low-pressure turbine stages. This erosion is exacerbated by high rotational speeds, leading to material loss and reduced aerodynamic efficiency.
Oxidation and Chemical Attack
Oxidation reactions degrade blade surfaces at elevated temperatures (above 600°C). Additionally, steam's acidic contaminants (e.g., sulfur compounds) accelerate chemical corrosion.
Cavitation Damage
Rapid pressure changes in steam flow create vapor bubbles that collapse violently, causing localized pitting and surface degradation.
Material Selection Criteria for Turbine Blade Wear Strips
To combat these challenges, materials must meet stringent requirements:
High-Temperature Stability: Retain hardness and strength at operating temperatures (up to 980°C).
Corrosion Resistance: Withstand acidic, alkaline, and oxidative environments.
Abrasion Resistance: Minimize wear from particulates and micro-droplets.
Low Friction Coefficient: Reduce adhesive wear and energy losses.
Compliance with Industry Standards: Ensure reliability through certifications like AMS 5894.
Why Alloy 6B/UNS R30016 is the Ideal Choice
Superior Composition
Alloy 6B’s cobalt-chromium-tungsten matrix (Co-Cr-W) provides intrinsic resistance to oxidation, sulfidation, and chloride-induced corrosion. Its high chromium content (~30%) forms a protective oxide layer, while tungsten enhances hardness and wear resistance.
Exceptional Mechanical Properties
Hardness: HRC 40–45 in the as-cast state, ensuring durability against abrasive wear.
Thermal Stability: Maintains structural integrity up to 980°C, critical for high-pressure turbine stages.
Low Friction: Reduces galling and adhesive wear in unlubricated environments.
AMS 5894 Compliance
Alloy 6B adheres to the AMS 5894 aerospace material specification, guaranteeing consistent quality and performance in critical applications. This standard ensures optimal alloy composition, heat treatment, and mechanical testing.
Proven Applications
Beyond turbine blades, Alloy 6B is widely used in:
Valve seats and pump components (resistance to cavitation).
Nuclear reactor components (radiation resistance).
Food processing equipment (non-toxic, hygienic properties).