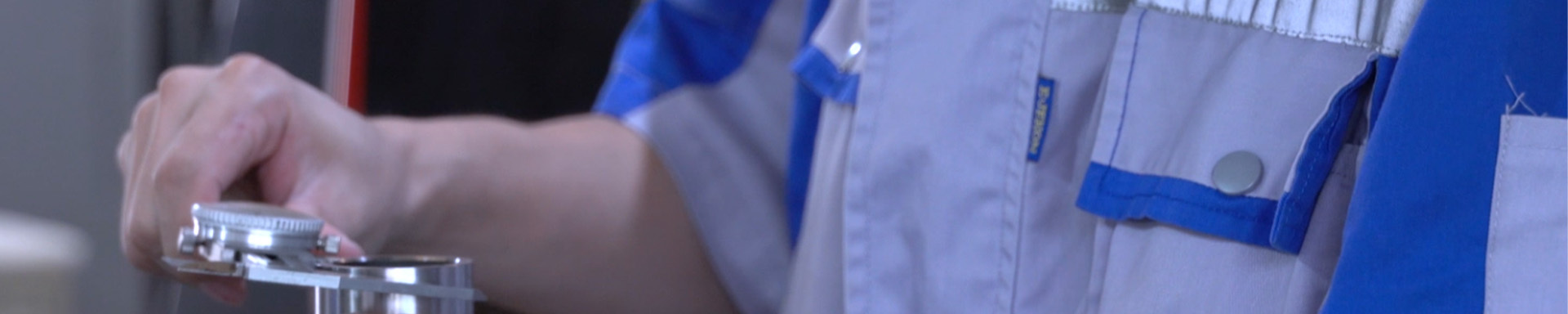
Why Cobalt Alloys Better than Nickel Alloys in High Temperature Vulcanizing Environments?
2025-03-26 09:00In high-temperature vulcanizing environments, the choice of material has a direct impact on the service life and stability of the equipment. Cobalt alloys are superior to many traditional nickel alloys in extreme conditions due to their excellent high temperature resistance, wear resistance, impact resistance and corrosion resistance. So what is it about cobalt alloys that gives them an advantage in high temperature vulcanization environments?
1. High Temperature Stability of Cobalt Alloys
Cobalt alloys, such as Alloy 6K, are able to maintain high strength and hardness below 900°C, which gives them good mechanical properties in high temperature environments. Their excellent resistance to oxidation at high temperatures is mainly due to the protective oxide film formed by chromium, which can effectively resist the erosion of high-temperature gases, sulfides and other corrosive media.
In contrast, although nickel alloys also have a certain degree of resistance to vulcanization in high-temperature environments, they rely on the synergistic effect of elements such as aluminum and molybdenum, which may lead to performance degradation under certain harsh operating conditions. Therefore, cobalt alloys are more stable under persistent high temperature vulcanization conditions.
2. Excellent wear and impact resistance
Cobalt alloys, due to their unique, uniformly distributed carbide structure, perform well under high stress, particle washout or sliding friction, significantly reducing component wear. Especially in high-temperature sulfide atmospheres, where the wear resistance of many materials decreases significantly, cobalt alloys still maintain low wear rates.
In addition, the toughness of the cobalt matrix provides excellent impact resistance to fatigue damage caused by alternating loads on mechanical components. This characteristic makes cobalt alloy an ideal material for manufacturing high-temperature wear-resistant parts such as valve seats, bearing bushings, impellers and sealing rings.
3. Excellent corrosion and oxidation resistance
The high chromium content of cobalt alloy makes it remain stable in acidic solution, seawater and high-temperature vulcanization environment, and it has strong corrosion resistance to nitric acid, organic acid and other chemical media.
Under high-temperature vulcanization conditions, sulfides are extremely aggressive to materials, and many metals are susceptible to sulfide corrosion or even fracture failure. However, cobalt alloys, by virtue of their special composition design, can effectively resist sulfide atmosphere at high temperatures, and are widely used in chemical reactors, marine equipment, petroleum refining devices and gas turbines and other fields.
In contrast, although the corrosion resistance of nickel alloys is better than that of many common metals, the corrosion resistance of certain nickel alloys is still limited under high-temperature sulfide environment, which makes it difficult to meet the requirements of long-time stable operation.
4. Optimized balance of composition and process
Cobalt alloys achieve a balance between high temperature resistance, wear resistance and corrosion resistance by precisely controlling the ratio of cobalt, chromium, tungsten, carbon and other elements. This material design enables it to maintain excellent overall performance under extreme working conditions, and is therefore widely used in aerospace, energy, petrochemical, steel smelting and high-temperature and high-pressure valves.
In contrast, while nickel alloys excel in certain specific applications, such as high strength, low coefficient of thermal expansion and excellent electromagnetic properties, they are less resistant to abrasion and impact in high-temperature vulcanized environments, and their overall performance is less stable than cobalt alloys.
Conclusion: Why cobalt alloys?
Taken together, cobalt alloys are superior to nickel alloys in high-temperature vulcanization environments with the following core advantages:
✅ Higher high temperature stability - can withstand high temperatures up to 900°C and mechanical properties remain stable.
✅ Better wear resistance - Carbides are uniformly distributed, allowing them to excel in frictional wear environments.
✅ Better Impact Resistance - The cobalt matrix gives the material good fatigue and impact resistance.
✅ Superior corrosion resistance - Excellent corrosion resistance is maintained in high temperature vulcanization, acidic and marine environments.
✅ More scientifically optimized composition - Achieves a balance of properties between heat, wear and corrosion resistance.
As a result, cobalt alloy is a more reliable choice for severe working conditions requiring high temperature, wear and corrosion resistance, and is widely used in critical fields such as chemical industry, energy, metallurgy and aerospace.
If you are looking for high performance cobalt alloy materials, welcome to contact us, SYTOP provides high quality cobalt alloy products to meet your special needs!