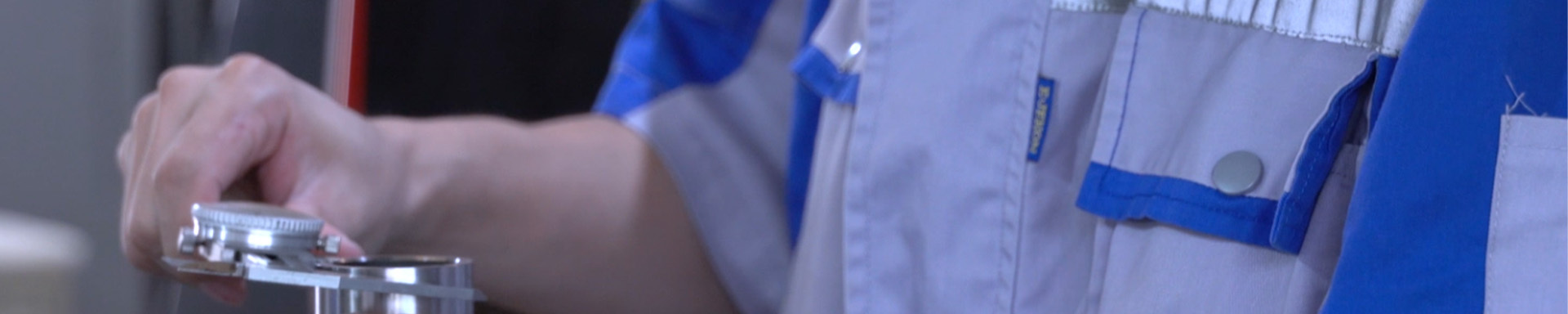
Cobalt Alloy 25 Haynes 25 Alloy L605 UNS R30605
2024-12-06 09:00Introduction to Cobalt Alloy 25 (Haynes 25, Alloy L605, UNS R30605)
Cobalt Alloy 25, commonly known as Haynes 25 or Alloy L605, is a high-performance cobalt-based alloy with excellent properties in high-temperature, wear, and corrosion-resistant environments. With a UNS number of R30605, this alloy is used in critical applications that demand superior strength, oxidation resistance, and durability. It meets the AMS 5337 and AMS 5759 standards.
Key Features and Applications of Cobalt Alloy 25
Cobalt Alloy 25 (Haynes 25, Alloy L605, UNS R30605) is often selected for aerospace, chemical processing, and industrial applications where components must endure extreme environments. The alloy maintains its mechanical properties even at high temperatures, making it a reliable choice for turbines, high-performance gas engines, and combustion chambers.
High-Temperature Resistance: Cobalt Alloy 25 offers exceptional stability and resistance to high-temperature environments, making it a preferred choice for turbine components and jet engines.
Corrosion and Oxidation Resistance: With its high cobalt concentration, Haynes 25 ensures excellent protection against oxidation and corrosion, even in high-stress environments such as exhaust systems, chemical reactors, and high-temperature sealing applications.
Mechanical Strength and Durability: Alloy L605 demonstrates remarkable mechanical properties, including high tensile strength and creep resistance at elevated temperatures, ensuring longevity and reliability in critical components.
Applications in Aerospace and Industrial Sectors: Common applications of Cobalt Alloy 25 include gas turbine blades, exhaust valves, and components exposed to extreme mechanical stresses. It is particularly favored in aerospace for its ability to perform under high-stress conditions and its extended lifespan under high-temperature cyclic conditions.
Advantages of Using Cobalt Alloy 25 (Haynes 25, Alloy L605, UNS R30605)
Versatility in Harsh Environments: The primary advantage of using Cobalt Alloy 25 is its unparalleled resistance to wear, corrosion, and oxidation, which makes it an ideal solution for industries like aerospace, power generation, and chemical processing. Its strength and durability in extreme conditions ensure long-term performance with minimal maintenance.
Standards Compliance: AMS 5337 and AMS 5759 are the aerospace standards that Cobalt Alloy 25 (Haynes 25) meets, ensuring customers that the material can be trusted for critical applications. These standards ensure the alloy has undergone rigorous testing to guarantee its reliability in aerospace and other high-performance industries.
Cost-Effectiveness in the Long Run: While the initial cost of Alloy L605 may be higher than other materials, the long-term benefits outweigh the costs. The alloy’s high resistance to wear and corrosion translates into longer-lasting components, reducing the need for frequent replacements and repairs. This ultimately leads to a cost-effective solution in demanding industries.
Why Choose Cobalt Alloy 25 (Haynes 25)?
Choosing Cobalt Alloy 25, also known as Haynes 25, Alloy L605, and UNS R30605, for high-temperature, wear-resistant applications offers multiple advantages, including improved performance, reduced maintenance, and a longer lifespan for critical components. This alloy is designed for extreme environments and performs exceptionally well in applications that involve high mechanical stresses and elevated temperatures.
Cobalt Alloy 25 is a trusted material known for its strength, durability, and resistance to oxidation and corrosion, whether used in aerospace turbine blades, gas engine parts, or chemical processing equipment.
Please visit our product page for more information about Cobalt Alloy 25, Haynes 25, Alloy L605, or UNS R30605.