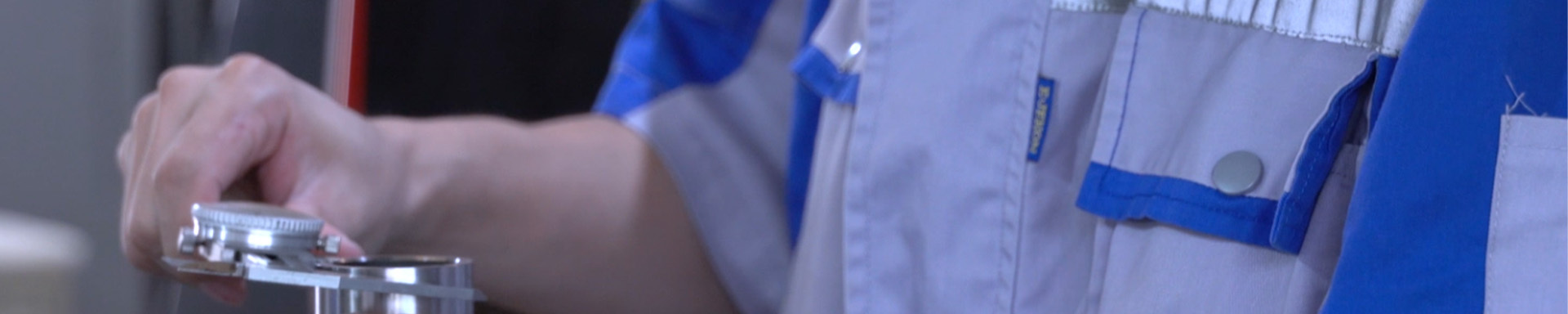
Are Your Operation Environments Suitable for Cobalt Alloys?
2025-02-13 09:00Core characteristics and applicable working conditions of cobalt-based alloys
1. Performance advantages in extreme environments
Cobalt-based alloys (cobalt-based, containing chromium, tungsten, molybdenum, and other elements) are particularly outstanding in the following scenarios:
High-temperature wear resistance: It can maintain high hardness and wear resistance above 800°C and is suitable for gas turbine blades, high-temperature valve sealing surfaces, etc..
Corrosion resistance and oxidation resistance: In acidic media or molten metal (such as zinc and lead) environments, the corrosion resistance is better than that of nickel-based alloys, such as chemical pumps and valves, electroplating rollers, etc..
Thermal fatigue resistance: Suitable for parts with frequent thermal cycles, such as aircraft engine combustion chamber lining.
2. Analysis of typical application scenarios
Energy and chemical industry: sunken roller sleeves, injection molding machine screws, high-temperature, and high-pressure valves, etc., which require both wear resistance and corrosion resistance.
Aerospace: high-temperature and high-strength parts such as turbine guide blades and combustion chamber components.
In medical and special industries, biocompatible alloys (such as ASTM F75) are used for artificial joints, and high-hardness alloys (such as W-21 with HRC58) are used in harsh wear environments.
Alternative solutions and brand selection guide
To avoid trademark restrictions, the following general brands or similar materials can be selected:
1. International standard brands
Cobalt-chromium-tungsten series, such as UNS R30006 and R30021, are suitable for high-temperature wear-resistant parts.
The cobalt-chromium-molybdenum series, such as UNS R30021, suits pumps, valves, and biomedical devices in acidic environments.
2. Domestic equivalent grades
GH series high-temperature alloys, such as GH5188 (corresponding to Haynes 188) and GH5605 (corresponding to L605), meet the high-temperature requirements of the aviation and energy fields.
Customized materials, such as Shanghai Rongkun Metal's W-21 alloy (HRC58), can replace traditional high-carbon cobalt-based alloys for molten metal corrosion protection.
3. Process compatibility
Forming technology: Powder metallurgy, precision casting, forging, and other processes can adapt to different morphological requirements (such as ultra-fine wire and precision castings).
Welding and repair: Cobalt-based welding wire (such as AWS A5.21 ErCoCr) for surfacing can efficiently repair worn parts.
Key considerations for material selection
Balance between cost and performance: Cobalt resources are scarce. It is recommended to prioritize nickel-based or iron-based alloys (such as Inconel 718) to meet medium temperature requirements through working condition analysis and only use cobalt-based materials under extreme conditions.
Third-party testing and certification: Ensure that the material meets standards such as ASTM B462, GB/T 14992, and is verified by authoritative institutions (such as the National Iron and Steel Materials Testing Center).
Supply chain efficiency: Select suppliers with semi-finished product inventory (such as delivery within two weeks) to shorten production cycles.
Industry case: successful alternative solution
A chemical company uses UNS R30006 alloy to manufacture high-temperature valve sealing surfaces. After replacing the original nickel-based alloy, the service life is increased by 3 times, while it can withstand corrosive media with a pH of 2 to 12, and the annual maintenance cost is reduced by 40%.
Cobalt-based high-temperature alloys are the "ultimate material" under complex working conditions, but alternative grades and processes must be selected based on specific needs. It is recommended that users work with material suppliers and testing agencies to conduct customized material selection analyses to maximize economic benefits and equipment reliability.