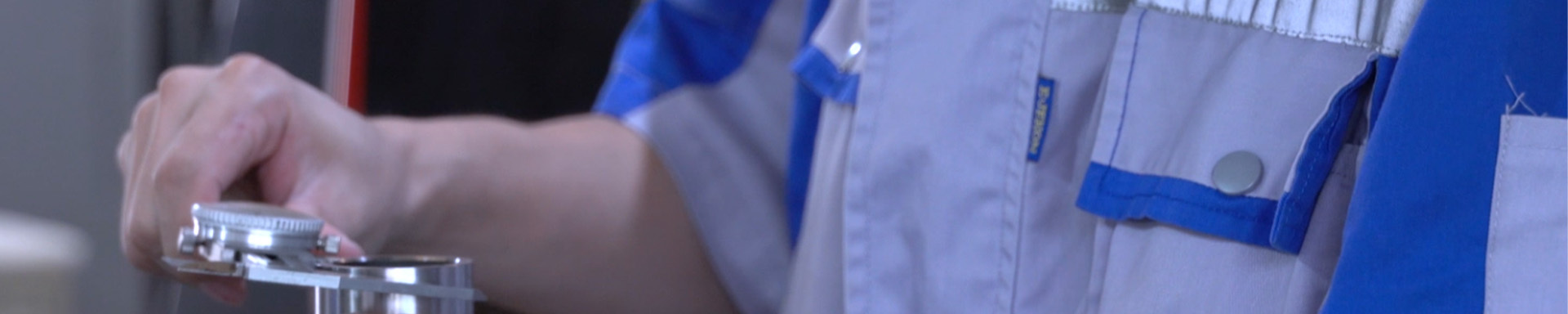
Applications of Cobalt 12# Alloy
2025-01-10 09:00Applications of 12 Alloy
Cutting and Wear Parts:
Cobalt12# Alloy is widely used for cutting tools and wear-resistant parts. Its ability to maintain sharpness and resist deformation under high pressure makes it ideal for:
Industrial knives.
Bandsaw blade tips.
Continuous Copper Extrusion dies.
Valve Components:
In the oil and gas industry, Cobalt 12# Alloy is often used for critical valve components like valve seats and balls, ensuring reliable operation under high pressure and corrosive conditions.
Aerospace Applications:
The alloy’s exceptional heat resistance suits it for turbine blades and other high-temperature components in aerospace engineering.
Welding and Hardfacing:
Cobalt 12# Alloy is frequently applied in hard facing to protect equipment surfaces from wear and tear, extending the life of machinery used in mining, power plants, and chemical processing.
Main Content:
Cobalt 12# Alloy: A Reliable Solution for Extreme Conditions
Cobalt 12 Alloy, a cobalt-based alloy, has earned a reputation for exceptional performance in demanding applications. With superior resistance to wear, heat, and corrosion, Cobalt 12 Alloy is a preferred material for industries such as oil and gas, aerospace, and manufacturing, where durability and reliability are paramount.
Composition and Key Properties
The composition of Cobalt 12# Alloy is carefully engineered to deliver optimal performance in extreme conditions. Its primary components include cobalt, chromium, and tungsten, which together provide:
High Wear Resistance: Ideal for applications with significant abrasion and friction.
Heat Resistance: Can withstand temperatures exceeding 800°C without losing strength or hardness.
Corrosion Resistance: Performs well in harsh chemical environments, including acidic and saline conditions.
These properties make Cobalt 12 Alloy a versatile material for various industrial uses.