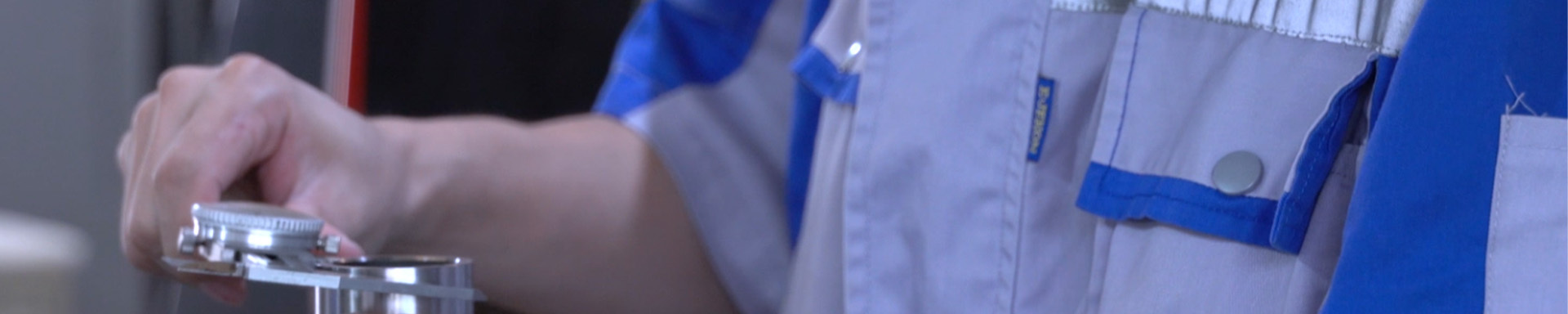
- Home
- >
News
Purchasing cobalt alloy requires a keen understanding of its properties and applications. As the demand for high-quality, wear and corrosion-resistant alloys grows, it's essential to know how to look for a supplier.
In the early weeks of July 2023, mining hubs worldwide, particularly in the Democratic Republic of Congo, witnessed an unexpected surge in cobalt prices. This sudden shift, triggered by a combination of increased demand and supply chain disruptions, has sent shockwaves through industries dependent on this crucial raw material
Co 12 is a cobalt-based alloy known for its exceptional wear, high temperature, and corrosion resistance. Its superior durability makes it a preferred choice for terrible environments in various industries.
Shenyang TOP is a leading manufacturer of cobalt based alloy, places a high priority on quality control and assurance measures to guarantee product reliability and consistency. The measures include strict control over raw material procurement, production processes, and comprehensive testing and inspection procedures. SYTOP continuously improves its processes to maintain high standards of quality and customer satisfaction.
Cobalt-chromium alloy used in pressurized water reactor (PWR) systems due to its excellent corrosion and wear resistance, radiation resistance, strength, and resistance to thermal fatigue. These properties ensure safe and reliable operation of PWRs, making cobalt alloy an essential material in nuclear power generation.
Except the company size and some necessary certificates, there are there important aspects need to be considered when you want to find a reliable supplier.
Cobalt-based alloys usually are described as wear-resistant, corrosion-resistant and heat-resistant alloys. Many of the alloy's properties arise from the crystallographic properties of cobalt (especially its response to stress), the solid solution strengthening effects of chromium, tungsten and molybdenum, the formation of metal carbides, and the corrosion resistance imparted by cobalt to chromium. Typically, softer and harder compositions are used for high-temperature applications, such as gas turbine blades and strips. Harder grades are used to resist wear.