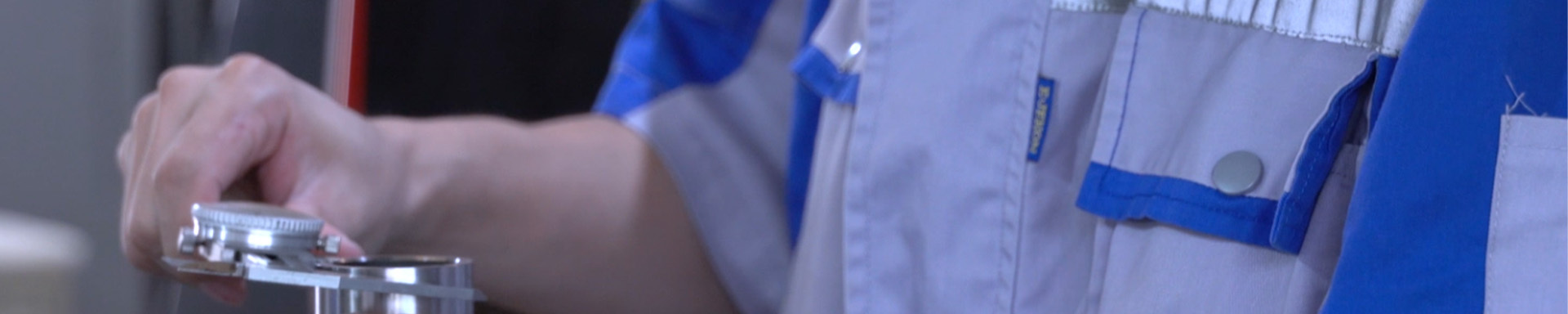
- Home
- >
- News
- >
- Cobalt Alloys
- >
Cobalt Alloys
2022-08-02 10:19Cobalt-Based Wear-Resistant Alloys
Cobalt-based wear resistant alloys are little changed from Elwood Haynes' earlier alloys. The most important difference has to do with the control of carbon and silicon (which were defects in earlier alloys). Indeed, the main difference in current Stellite alloy grades is the carbon and tungsten content. Carbon content affects hardness, ductility and wear resistance. Tungsten also plays an important role in these properties.
There are several different types of wear, generally divided into three broad categories:
Abrasive wear
sliding wear
Corrosion wear
The type of wear encountered in a particular application is an important factor in the selection of wear resistant materials.
Abrasive wear occurs when hard particles or hard protrusions (on the opposite side) are forced against and move relative to the surface. High-stress wear and low-stress wear involve the state of the abrasive media (whether hard particles or protrusions) after interacting with the surface. If an abrasive medium is crushed, it is said to be in a state of high stress. If the grinding media remains intact, the process is called low stress wear. Typically, high-stress wear is caused by hard particles being sandwiched between metal surfaces (relative motion), while low-stress wear is encountered when moving surfaces come into contact with packed abrasives such as soil and sand.
In alloys containing a hard phase, such as cobalt-based wear-resistant alloys, wear resistance generally increases with the volume fraction of the hard phase. However, wear resistance is strongly influenced by the size and shape of the hard phase precipitates within the microstructure in the hard structure and the size and shape of the corrosion species.
Sliding is probably the most complex and is not a conceptual issue, but rather how different materials respond to sliding conditions. Sliding wear can occur whenever two surfaces are pressed together and moved relative to each other. If both surfaces are metallic in nature and have little or no lubrication, the chance of damage is greatly increased.
Cobalt-Based High-Temperature Resistant Alloys
For many years, the main user of superalloys has been the gas turbine industry. For aircraft gas turbines, the main material requirements are high temperature strength, thermal fatigue resistance and oxidation resistance. Sulfur resistance is a major concern for land-based gas turbines that typically burn low-grade fuels and operate at lower temperatures.
Cobalt-Based Corrosion Resistant Alloys
Although cobalt alloys have some resistance to water corrosion, they are limited by grain boundary carbide precipitation, lack of important alloying elements in the matrix (after carbide or Laves precipitation), and in the following situations: casting and Weld surfacing material.
Due to their uniform microstructure and lower carbon content, deformed cobalt-based superalloys (which typically contain tungsten instead of molybdenum) are more resistant to water corrosion, but are still much less corrosive than nickel-chromium-molybdenum alloys.
To meet the industrial demand for alloys with excellent resistance to water corrosion while at the same time having the properties of cobalt as the basis of the alloy (resistance to various forms of wear and high strength over a wide temperature range) , forging several low carbon alloys to produce cobalt-nickel-chromium-molybdenum alloys.