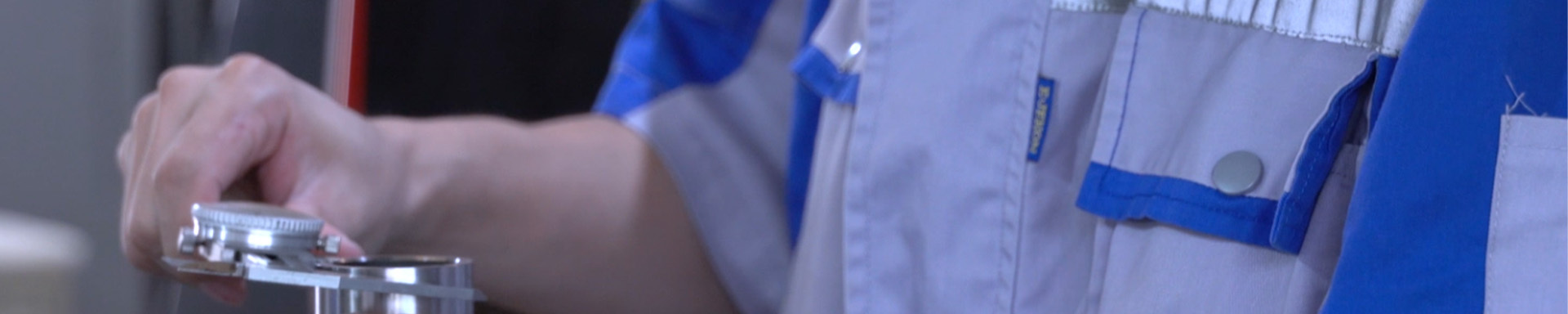
- Home
- >
News
Cobalt alloy is widely utilized across various industries, owing to its superior properties such as excellent wear resistance, corrosion resistance, and high-temperature durability. This article primarily delineates the advantages of cobalt alloy compared to other alloys and its applications in different fields.
Cobalt alloys play a crucial role in the galvanizing industry. This article primarily discusses the specific products of Cobalt alloys in the galvanizing industry and the common components used in galvanizing industry.
SYTOP will be presenct at CIPPE, offering insights into the latest advancements in Coblat alloy technology. Engage with our experts at Booth No. W3245 in Hall W3 to discover innovative solutions tailored to meet your specific industry needs.
Cobalt alloy 6K, a game-changer in knife-making, is earning its place among renowned knifemakers for its unique blend of rust-resistance and wear-resistance.
Cobalt-chromium alloy used in pressurized water reactor (PWR) systems due to its excellent corrosion and wear resistance, radiation resistance, strength, and resistance to thermal fatigue. These properties ensure safe and reliable operation of PWRs, making cobalt alloy an essential material in nuclear power generation.
Cobalt-based alloys usually are described as wear-resistant, corrosion-resistant and heat-resistant alloys. Many of the alloy's properties arise from the crystallographic properties of cobalt (especially its response to stress), the solid solution strengthening effects of chromium, tungsten and molybdenum, the formation of metal carbides, and the corrosion resistance imparted by cobalt to chromium. Typically, softer and harder compositions are used for high-temperature applications, such as gas turbine blades and strips. Harder grades are used to resist wear.