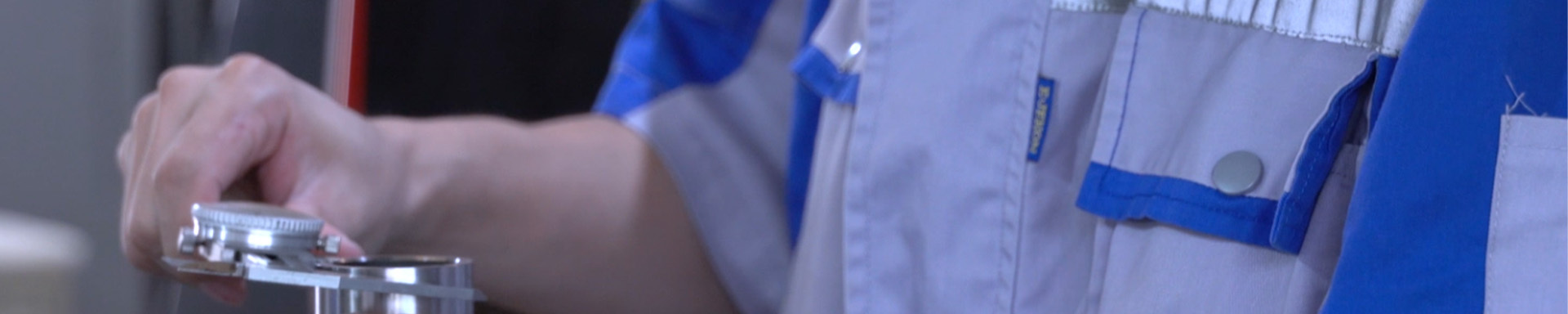
Commonly AWS A5.21 Welding Rods
2022-08-08 15:52Common Cobalt alloy grades include:
Cobalt Alloy 1 welding rods is equal to AWS ErCoCr-C
High carbon Co-Cr-W alloy surfacing welding wire has good wear resistance and corrosion resistance, but poor impact toughness.
It mainly used for surfacing welding of wear parts such as roller cone bit bearings, boiler rotating blades, etc.
Hardness of surfacing layer: HRC≥52
Cobalt Alloy 6 welding rods is equal to AWS ErCoCr-A
Cobalt Alloy 6 welding rods is the one with the lowest C and W content and the best toughness among Co-Cr-W butt welding alloys.
It can withstand impact under hot and cold conditions, has a small tendency to crack, and has excellent corrosion resistance, heat resistance and wear resistance.
Mainly used to maintain good wear resistance and corrosion resistance when working at high temperature, such as high temperature and high pressure valves, hot forging dies, etc.
Hardness of surfacing layer: HRC 40-45
Cobalt Alloy 12 welding rods is equal to AWS ErCoCr-B
Cobalt Alloy 12 welding rods has medium hardness and good wear resistance in surfacing alloys, but poor plasticity, good corrosion resistance, heat resistance and wear resistance, and can still maintain these characteristics at high temperature of 650℃.
It is mainly used for surfacing welding of high temperature and high pressure valves, internal combustion engine valves, high pressure pump bushings and lining sleeves, hot roll pass patterns, etc. Also used for surfacing on the tip of band saw teeth in the wood industry.