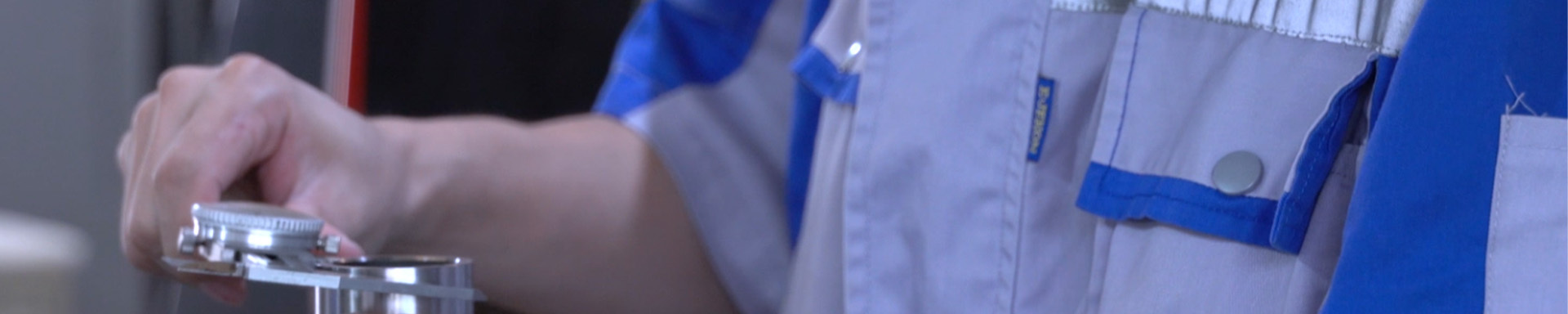
What's the Difference Between Wallex® and Colmonoy® Hardfacing?
2024-11-01 09:00Hardfacing refers to a metalworking process in which a harder material is applied to a base material for enhanced protection. While it is primarily used to combat wear, it also offers defense against corrosion and impact damage. Various methods are employed for weld overlay, including thermal spraying, laser cladding, and traditional welding. In cases of severe wear, weld overlay coatings are often preferred due to their strong metallurgical bond.
The two most common material families utilized in this process are cobalt alloys and nickel alloys. In the following discussion, we will examine the most prevalent types within these families, Wallex® and Colmonoy®, explore their differences, and identify the most suitable applications for each.
Wallex® is cobalt-based alloys, Colmonoy® is nickel-based alloys. Both consist of alloys that contain varying amounts of additional elements, including carbon, chromium, boron, silicon, iron, molybdenum, and sometimes tungsten carbide. Most alloys in each family can be applied using thermal spraying, welding, or a combination of spraying and fusing.
The main difference between Wallex® and Colmonoy® coatings is their hardness. As is typical with hardfacing solutions, increased hardness often results in reduced ductility. Nickel-based coatings are generally harder and perform better under abrasive wear conditions, but they may be prone to cracking under impact wear. In contrast, cobalt-based coatings exhibit greater ductility and better resistance to impact wear.
Cobalt-based coatings are frequently used for valve stems, bushing, piston rods, and similar applications due to their high-temperature wear and corrosion resistance. However, some users may opt for nickel-based coatings because of their good performance and lower cost. Nickel-based coatings offer excellent protection in harsh abrasive environments, such as those found in material-handling screw conveyors. Other nickel-based hard-facing coatings applications include valve seats, ball valves, and various components. Both material families have a wide array of applications across different industries.
It is advisable to use solid cobalt or nickel alloy materials for optimal performance, as they provide high wear protection in demanding abrasive conditions. For additional questions, consulting a professional manufacturer is recommended.