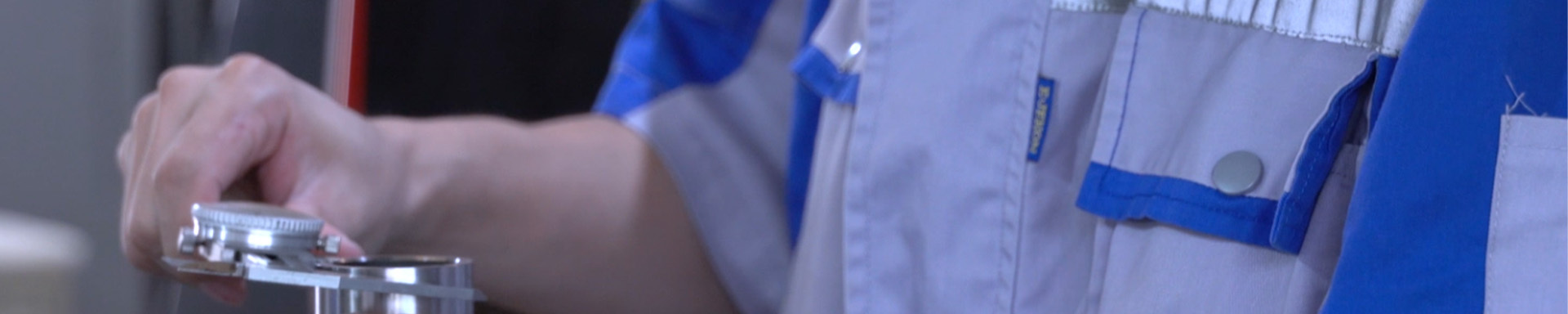
- Home
- >
- News
- >
- Cobalt Alloy VS 316L
- >
Cobalt Alloy VS 316L
2024-10-17 15:00Cobalt alloys are well-known for their ability to withstand extreme wear, high temperatures, and corrosion. Adding elements like chromium and tungsten gives these alloys enhanced durability, making them ideal for aerospace, power generation, and oil & gas applications.
Critical Advantages of Cobalt Alloys:
Wear Resistance: Cobalt alloys are challenging and offer superior protection against abrasive conditions.
High-Temperature Stability: These alloys maintain strength and stability even under extreme heat.
Corrosion Resistance: Cobalt alloys are highly resistant to corrosive environments, even in chemically aggressive settings.
316L stainless steel is famous for its excellent corrosion resistance and weldability. It is commonly used in chemical processing and marine environments. The "L" in 316L indicates a low carbon content, enhancing corrosion resistance, especially in welded structures.
Critical Advantages of 316L:
Corrosion Resistance: 316L protects against rust and corrosion, particularly in chloride-rich environments.
Weldability: Its low carbon content makes it ideal for welding, as it minimizes carbide precipitation.
Cost-Effective: Compared to cobalt alloys, 316L is generally more affordable and more accessible to source.
Cobalt Alloy VS 316L
Cobalt alloys are far superior in terms of wear resistance. While 316L offers good durability in many applications, it cannot match cobalt alloys' hardness and long-term wear protection. This makes cobalt alloys the preferred choice for high-friction environments.
When it comes to extreme temperatures, cobalt alloys are the clear winner. They retain their strength and structural integrity even in high-heat conditions, making them ideal for jet engines, turbines, and other high-temperature machinery. 316L is more suited to moderate-temperature applications.
Both materials offer excellent corrosion resistance, but their effectiveness depends on the environment. Cobalt alloys can handle more aggressive chemical environments, whereas 316L performs well in saline or mildly corrosive settings, such as marine applications.
316L stainless steel is generally more affordable than cobalt alloys, making it a good choice for cost-sensitive projects. However, the higher upfront cost of cobalt alloys is often justified by their longer lifespan and enhanced performance in demanding conditions.
Which Material Should You Choose?
The choice between cobalt alloy and 316L depends on the specific requirements of your application. Cobalt alloys are the superior choice if your project demands exceptional wear resistance, high-temperature stability, or resistance to aggressive corrosion. On the other hand, if cost, ease of welding, and general corrosion resistance are more critical, 316L may be the better option.
At SYTOP, we specialize in manufacturing high-quality cobalt alloy products for various industries. Explore our range of cobalt alloy components and discover how they can meet your demanding application needs. Visit our product page for more information.