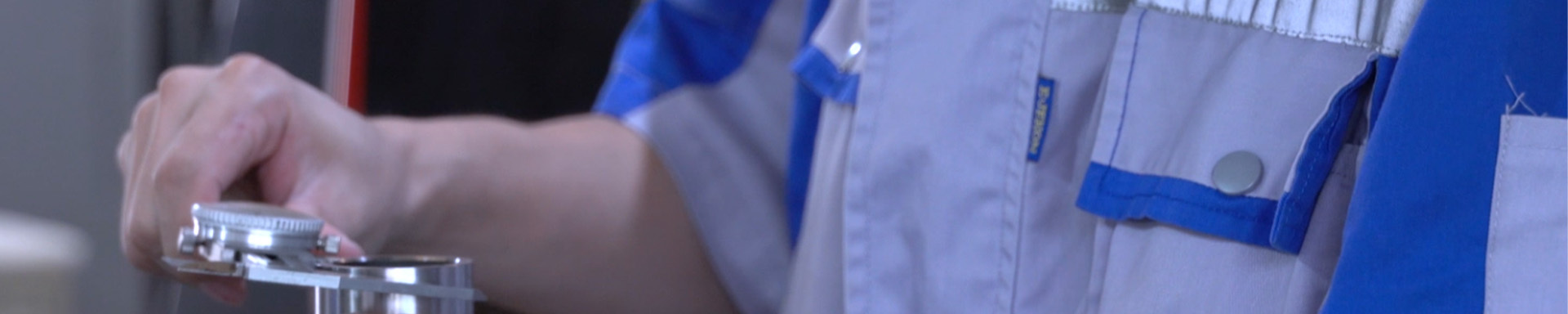
Application of Cobalt Alloys in the Oil and Gas Industry
2024-08-22 11:00As a superalloy, cobalt alloys are known for their excellent wear, corrosion, and high-temperature resistance. These unique properties make them indispensable materials in extremely harsh environments, especially in the oil and gas industry.
1. Importance in the Oil and Gas Industry
The operating environment of the oil and gas industry is extremely harsh, and materials need to withstand the test of extreme temperatures, high pressures, and corrosive environments for a long time. With their excellent wear and corrosion resistance, cobalt alloys play a crucial role in ensuring the reliability and efficiency of tools and equipment in exploration, drilling and production processes.
2. Composition of Cobalt Alloys
Cobalt alloys are based on cobalt as the base metal and are strengthened by adding elements such as chromium, nickel, tungsten, or molybdenum. This diverse combination gives cobalt alloys a variety of excellent properties.
3. Types of Cobalt Alloys Used in Industry
Given the special environment of the oil and gas industry, cobalt alloys are extremely rich in types and shapes. From simple bars and plates to complex parts, we can tailor them according to customer needs to ensure that each equipment can get the most suitable cobalt alloy solution.
4. Key Performance and Characteristics
Cobalt alloys are particularly resistant to wear, corrosion and high temperature. They can maintain hardness and resist oxidation at high temperatures, making them an ideal choice for key components such as drill bits and valves in the oil and gas industry.
5. Application Products in the Oil and Gas Industry
Cobalt alloys play an important role in drilling, exploration, completion and production in the oil and gas industry, helping to solve complex working conditions, improve equipment efficiency and reduce failures.
5.1 Drilling and Exploration
During underground operations, equipment and tools often fail due to wear or corrosion, which seriously affects production efficiency and increases maintenance costs. Cobalt alloys excel in resisting wear and corrosion and can effectively extend the service life of critical components and improve overall operating efficiency. In measurement while drilling (MWD)/logging while drilling (LWD) systems, cobalt alloys are widely used to manufacture flow distributors, orifice plates, inserts, correctors, turbine sleeves, blades, rotors, stators, nozzles, cages and cross bodies.
5.2 Solids Control Equipment: Centrifuge
The wear-resistant lining, cone and sleeve components in the centrifuge are made of cobalt alloys, which can withstand the extreme stress and wear environment in centrifugal operations. These components' long life and low maintenance characteristics make cobalt alloys the preferred material for reliability and durability.
5.3 Completion and production equipment
Cobalt alloy products also play an essential role in the completion and production stages. They are used to manufacture components such as valve seats, flow control devices and seals, which show excellent strength, wear resistance and corrosion resistance in high pressure, high temperature and corrosive environments. The application of cobalt alloys ensures the reliable operation of equipment, extends service life and reduces downtime, thereby ensuring the safety and efficiency of downhole operations.
In summary, cobalt alloys play an indispensable role in the oil and gas industry and have won wide recognition in the industry for their excellent durability, wear resistance, and high-temperature stability. We can provide customized cobalt alloy solutions according to your specific needs.