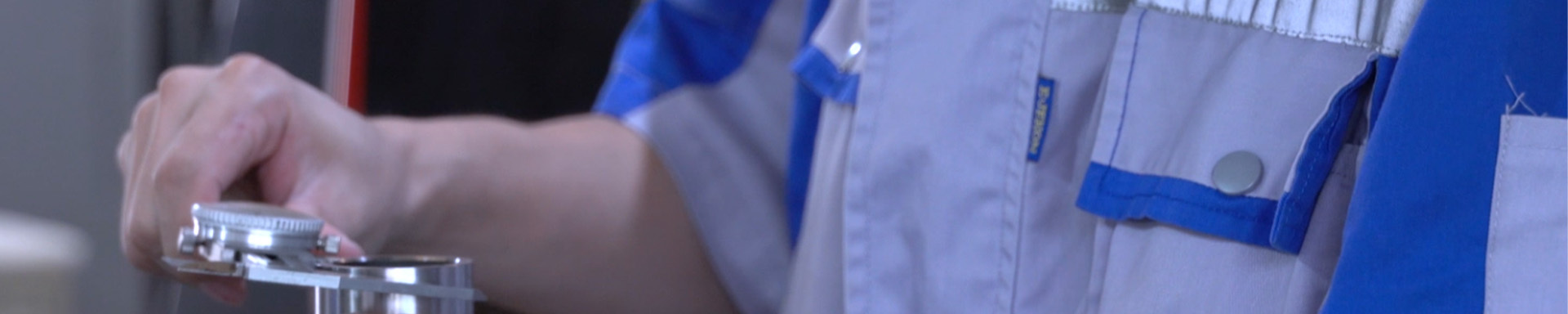
Cobalt Alloy Grade UNS R30006 High Temp Wear and Corrosion Alloy
2024-06-26 09:00UNS R30006, or Cobalt Alloy Grade 6, falls under the Unified Numbering System for metals and alloys, standardizing material designations across different industries. This cobalt alloy is characterized by its impressive resistance to wear and corrosion and high-temperature stability. Its composition typically includes a significant percentage of cobalt, chromium, tungsten, and a small amount of carbon. These elements work synergistically to provide the alloy with its outstanding properties.
Relationship with Other Cobalt Alloys
Cobalt alloys, in general, are renowned for their excellent mechanical properties and resistance to harsh conditions. UNS R30006 is a member of the group of cobalt-chromium alloys. This family of alloys is specifically designed to withstand severe wear and corrosion while maintaining strength at high temperatures. The primary advantage of UNS R30006 over other materials is its ability to maintain hardness and resistance to galling under thermal stress, making it ideal for cutting tools, turbine blades, and valve seats.
Comparison with Other Materials
Compared to other high-performance materials, such as stainless steel or nickel-based superalloys, UNS R30006 exhibits superior wear resistance. Stainless steels, for instance, offer good corrosion resistance but may lack the same level of hardness and wear performance under extreme conditions. While excellent at high temperatures, nickel-based superalloys can be more susceptible to wear. UNS R30006 provides a balanced solution, offering high-temperature performance and wear resistance.
Introduction to UNS R30016
UNS R30016 is another notable cobalt alloy within the Unified Numbering System. This grade, often called Cobalt Alloy 16, is designed for applications requiring enhanced corrosion resistance, particularly in acidic environments. Its composition typically includes higher chromium content, which enhances its corrosion-resistant properties, making it suitable for chemical processing and marine environments.
Detailed Comparison: UNS R30006 vs. UNS R30016
While both UNS R30006 and UNS R30016 belong to the cobalt alloy family, they are optimized for different applications. UNS R30006 is tailored for wear resistance and high-temperature stability, whereas UNS R30016 focuses on corrosion resistance. The higher chromium content in UNS R30016 allows it to perform better in corrosive environments, but it may not offer the same level of wear resistance as UNS R30006. Therefore, the choice between these two alloys depends largely on the application's specific requirements, such as whether the primary concern is wear or corrosion.
Applications and Industry Usage
The unique properties of UNS R30006 make it indispensable in industries like aerospace, where components are exposed to extreme conditions. Its usage extends to medical devices, oil and gas, and automotive industries where durability and performance are critical. On the other hand, UNS R30016 finds its applications in environments where chemical stability is paramount, such as chemical processing plants, desalination plants, and other marine applications.
Cobalt Alloy Grade UNS R30006 stands out for its remarkable wear and corrosion resistance at high temperatures, making it a superior choice for demanding applications. Its role within the cobalt alloy family, alongside other grades like UNS R30016, highlights the versatility and adaptability of cobalt-based materials. Understanding these alloys' specific properties and applications allows industries to make informed decisions, ensuring optimal performance and longevity of their components.