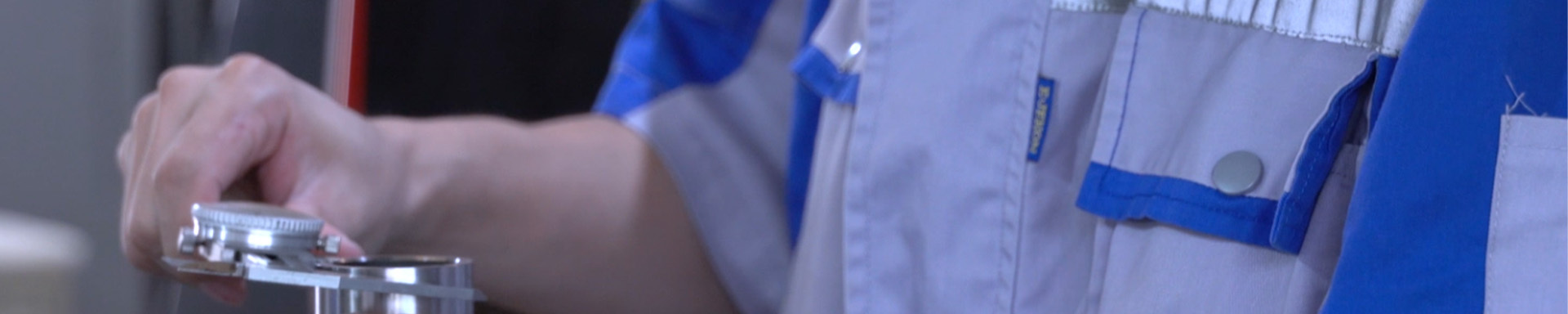
Main Components and Strength of Cobalt Alloy
2022-07-11 09:56Cobalt Alloy is a cemented carbide resistant to all types of wear and corrosion as well as high-temperature oxidation. commonly known as cobalt-based alloys, because cobalt alloy are mainly composed of cobalt, containing an amount of nickel, chromium, tungsten and a small amount of alloying elements such as molybdenum, niobium, tantalum, titanium, lanthanum, and occasionally iron. According to the different components in the alloy, they can be made into welding wire, powder used for hard surface surfacing, thermal spraying, spray welding and other processes, and can also be made into castings and forgings and powder metallurgy parts.
Cobalt alloys have good thermal corrosion resistance. It is generally believed that the reason why Cobalt alloys are better than nickel-based alloys in this respect is that the melting point of cobalt sulfides is higher than the melting point of the nickle sulfide (such as the eutectic temperature of Co-Co4S3 is 877°C, the eutectic temperature of Ni-Ni3S2 is 645 ° C), and the other reason is that the diffusivity of sulfur in cobalt is much lower than that in nickel.
The thermal stability of carbides in cobalt alloys is good. When the temperature rises, the growth rate of carbide agglomeration is slower than the growth rate of the γ phase in the nickel-based alloy, and the temperature of re-dissolving in the matrix is also higher (up to 1100 ℃), so when the temperature rises, The strength of cobalt alloys generally decreases slowly.
The size and distribution of carbide particles and grain size in cobalt alloy are very sensitive to the casting process. In order to achieve the required permanent strength and thermal fatigue properties of cast cobalt alloy parts, the casting process parameters are controlled. cobalt alloys need to be heat treated, mainly to control the precipitation of carbides.